Table of Contents
Tracking and Using Consumable Inventory
Updated
by Mitchell Paul-Soumis
Read Time: 6 mins
What are Consumable” items
A Consumable Item is any inventory that, once used or installed, will not be recovered and used again. However, not all Consumable items are handled the same way. Some Consumable Items will require specific tracking to monitor how they're being used, while others are simply added to track them for reordering as they're used.
Consumable items will occupy space in your warehouse or on vehicles in your fleet, and it's beneficial to track not only their existence, but also their rate of consumption. Some examples of common Consumable Items are:
- Satellite Dishes or antennas
- Power cords for rented Customer Premises Equipment
- Power tools and other installation equipment
Basics of tracking consumable items
If you're familiar with the inventory system in Sonar, you'll know that new Inventory Models can be added as a “Consumable” type. The Generic tag indicates the ability to add items to this model without defining fields, such as a Serial Number or MAC Address. The advantage of this approach is that it allows you to add traditionally difficult to track items without needless complexity. Below, we'll go through an example of how you might add and track a basic Consumable Item.
The item being added in the example is a bulk bag of RJ-45 terminations, but you could use some of the following item types for the same effect:
- Boxes of screws, nails, and other fasteners.
- Assigning several of these to a truck is very common, and having even more in the warehouse is equally so. Using this method to track these boxes lets you know when to add more to a truck, or order more to the warehouse.
- Containers of Cable Management Clips and Organizers
- Boxes of replacement parts or small miscellaneous items
In-depth example: Basic Consumable
In this example, the most common use of Consumable items will be covered. This use case covers scenarios where a Consumable item is being added to track your total amount to ensure that the item(s) can be reordered before you're completely out of that item in your warehouse. To follow along with this scenario, you'll have to have configured the Manufacturer and the Category of inventory.
- Add your Inventory Model. For this scenario, it will be named
RJ-45 Terminations - Bulk Bag
. - Once the Inventory Model is added, you can add items. These items will need an assignee and a quantity. For this scenario, we'll be assigning a bag to one of the technician's vehicles.
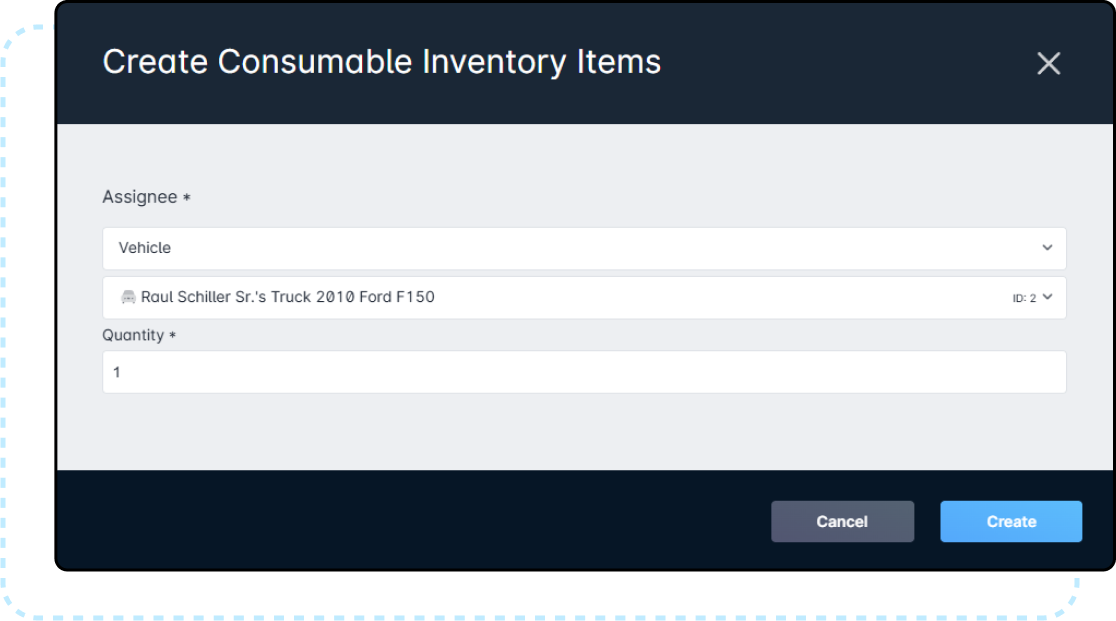
Once the item is completely consumed, a new, identical item can be moved from your warehouse assignee to the vehicle in Sonar, at the same time as it's moved from your physical warehouse to the physical truck.
Advanced tracking methods
Another way of tracking Consumable items is monitoring how more expensive items are consumed. While still not having any identifying fields to facilitate their addition as regular inventory, and generally not being recovered as customers churn or change services, they still require more tracking than the previous example.
Some examples of where you might track the usage of Consumable Items more closely are:
- Satellite or Radio mounting hardware
- Specialty hardware and fasteners
In-depth example: Tracking the Usage of Satellite J-Arms
In this example, a Consumable Inventory Model will be created that, when an item is assigned to a truck, will be monitored for its overall usage. This will be done to ensure that not only is there an accurate count of consumed items, but also that there is an accurate timeline to inform re-order requirements. The created Model will still be Consumable. The difference is simply in the diligence of the tracking efforts being employed. To follow along with this scenario, you'll have to have configured the Manufacturer and the Category of some Inventory Items already.
- Add your Inventory Model. For this example, the model will be named
Satellite/Antenna Bracket/Mount - 19"
with a display name ofJ-Arm - 19"
. - Once the Inventory Model is added, you can add items. These items will need an assignee and a quantity. For this scenario, the items would be assigned in batches of 5 to a technician's vehicle.Because we've added this item as a Generic Model, the only options are to add an item or set a vendor, no deployment types, fields, or LTE Provisioning is available for Generic Items
- As the items are installed at customer homes, your technicians will consume the inventory, indicating that they've been used.
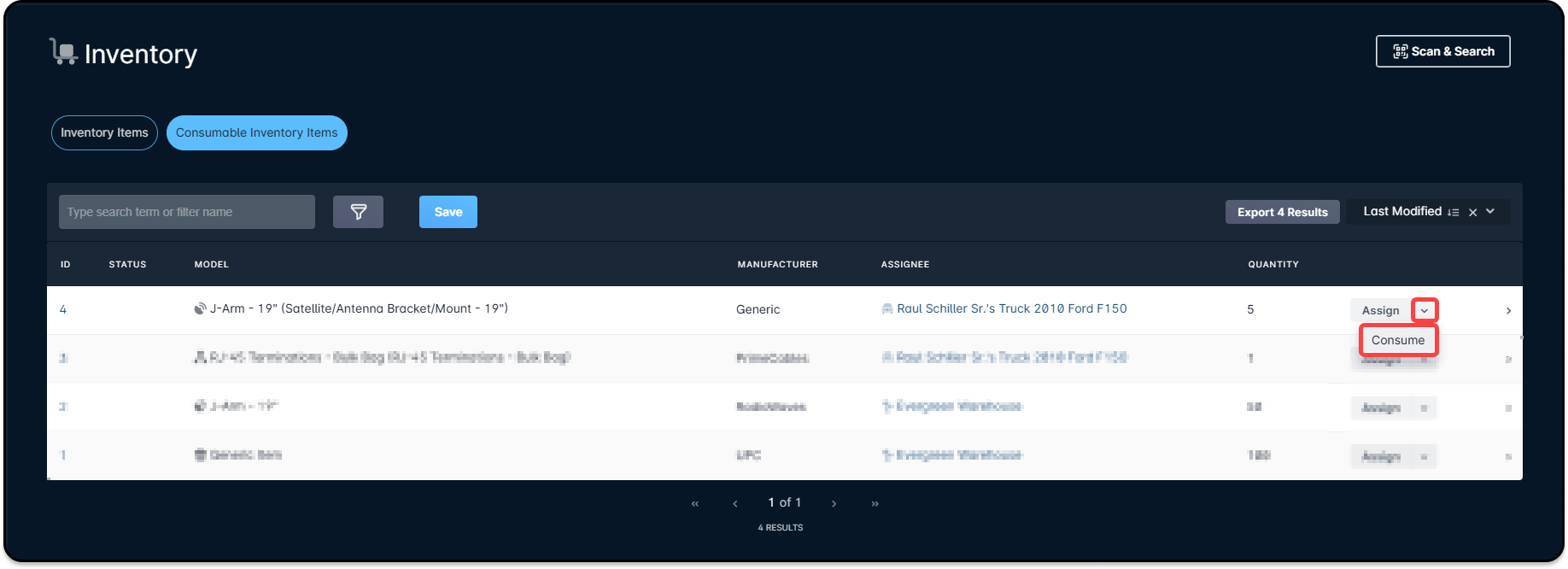
Monitoring Consumption
Where this method differs from the first, more basic, method shown is in the act of tracking the Inventory Items and their consumption. By tracking and consuming the inventory, we're not only tracking what gets used, but exactly how much. Unfortunately, this method does have a drawback:
- It's difficult to keep track of exactly where the inventory was consumed. For example, in the above scenario where the inventory was consumed on a job, there's no easy way to historically track where the inventory was consumed.
- You can optionally assign the inventory to the address or network site where the job was performed, then consume that inventory, however, this would result in an entity permanently listed under the consumable item with 0 units of inventory.
- You could alternatively record the consumed inventory on a custom field, but this would require additional manual processing for the field technician
Monitoring consumption works best when paired with the Inventory report. Consumable Inventory added to a vehicle or assigned to a technician is tracked and stored in a unique category of the Inventory Report. Using scheduling, you can have the report run at your preferred frequency, providing up-to-date statistics for how many units are used by a given installer.
In the J-Arm example above, a technician who frequently requires more frequent inventory assignment to their vehicle, and using the Inventory Report, you can monitor how many they used on a specific job. Outliers can be examined, and usage habits, or incorrect usage, can be corrected.
Benefits of Monitoring Consumable Item Usage
While not all items require specific tracking, this method does have a few advantages over the standard item tracking we explored in Scenario 1, especially when used in a non-traditional way.
- One advantage is for specific items, like boxes of screws — if a particular screw type is stored within a specific bin in your warehouse, by combining the count of consumable items with the bin, you'll always know when the number of screws starts getting low, allowing you to top up and add more to that bin.
- Another advantage of using the more precise Consumable Item tracking is the reduction in duplicate purchases. By keeping very close track of the items as they're consumed in Sonar, it removes the guesswork from restocking key consumable items.
In summary, while most users will find the first method of tracking consumable inventory more than sufficient, there are still possible use cases for tracking consumable items with even more precision. You may find the best method is a combination of both, depending on the nature of the item being tracked and consumed.